4design engineers every product in 3D CAD to optimise mechanics, maximise productivity and meet stringent regulatory standards.
Engineering is where every aspect of the product is resolved. How these details are implemented will determine the products performance, aesthetics, manufacturability and ultimate commercial success.
We run multiple 3D CAD platforms to ensure we have the flexibility to choose the best tool for your product.
Our engineering team is an experienced and accomplished group of very clever implementors, with significant experience across every manufacturing process.
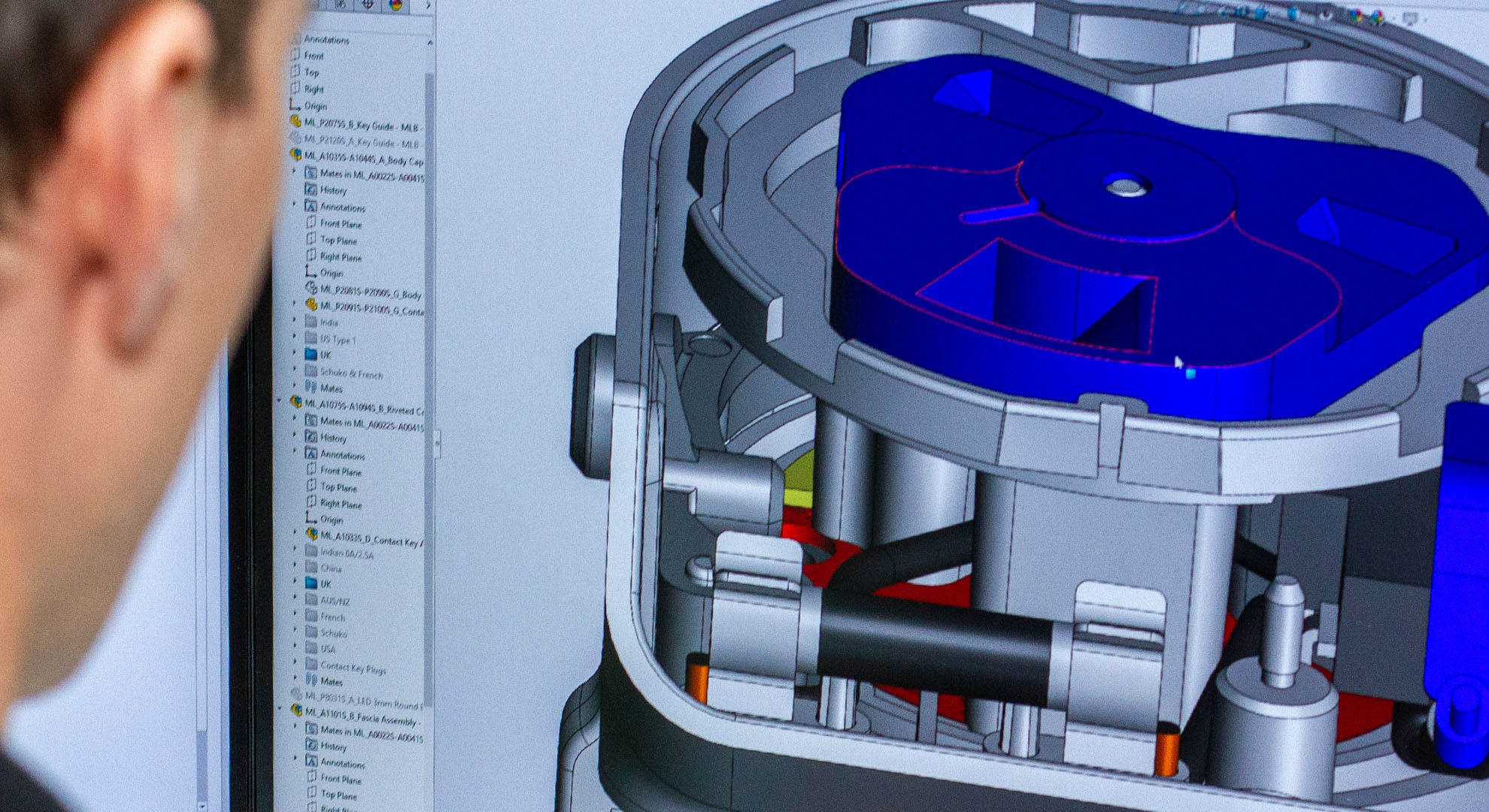
4design has engineered a number of products to comply with the global ingress protection (IP rating) XX standards for dust and water protection. Developing water and dust resistant products relies on an understanding of the precise engineering details to meet each rating. Over engineering can increase the BOM cost, under engineering can lead to product failure, so getting the balance right is absolutely key.
4design’s experience includes –
- Gasket engineering and compression requirements to suit dripping, sprayed or submerged water pressure.
- Material selection to maintain consistent seals under various environmental conditions. Temperature etc
- Static vs Dynamic loading of seals ie. Switches, buttons etc.
- Simplification of product assembly and part costs.
- Production methods, tolerancing and quality control standards to produce reliable and consistent parts.
- Authorised Testing laboratories for certified IP testing.
- High quality suppliers specialising in custom seals, orings, gaskets and foams etc
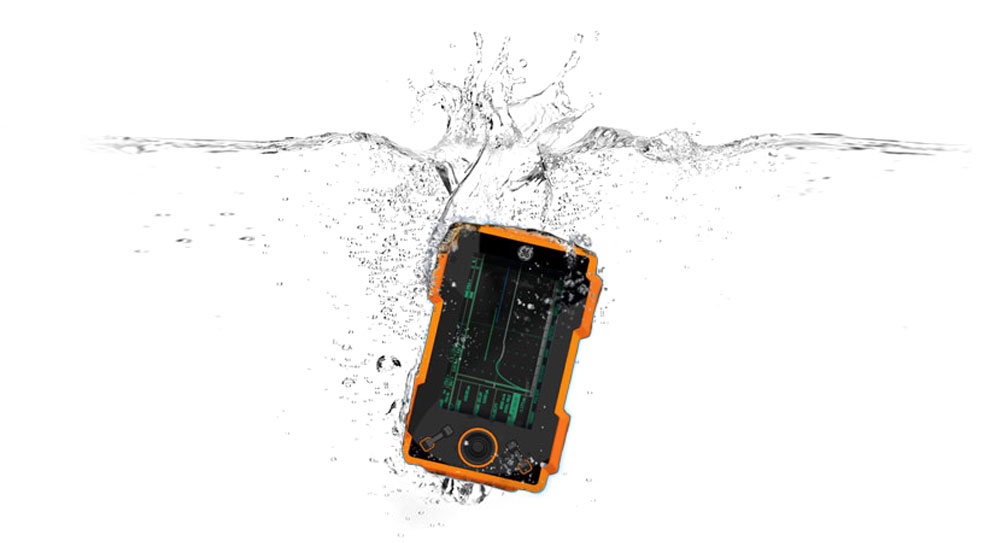
Thermal management is a key consideration in the design process as technology continues to become smaller, faster and more powerful. At 4design we use the latest thermal analysis techniques to predict product performance and improve product functionality and reliability.
We can help overcome thermal related problems found commonly in products including overheating and excessive thermal stress. Our thermal analysis services will help with the selection of the materials, processes and technologies, optimisation of the product’s weight, positioning of components and optimisation of heatsinks or fans based on the environment.
4design understand the differences and limitations between convection and fan forced cooling systems and can advise on the optimum solutions for your application.
Every product is different and has their own unique set of requirements however the fundamental principles of thermal dynamics are based on physics and these principles are both complex and consistent across all products.
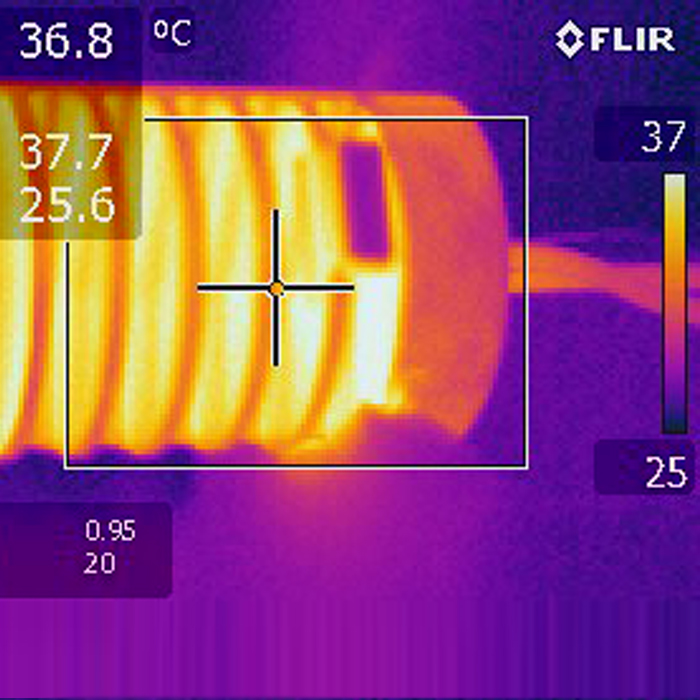
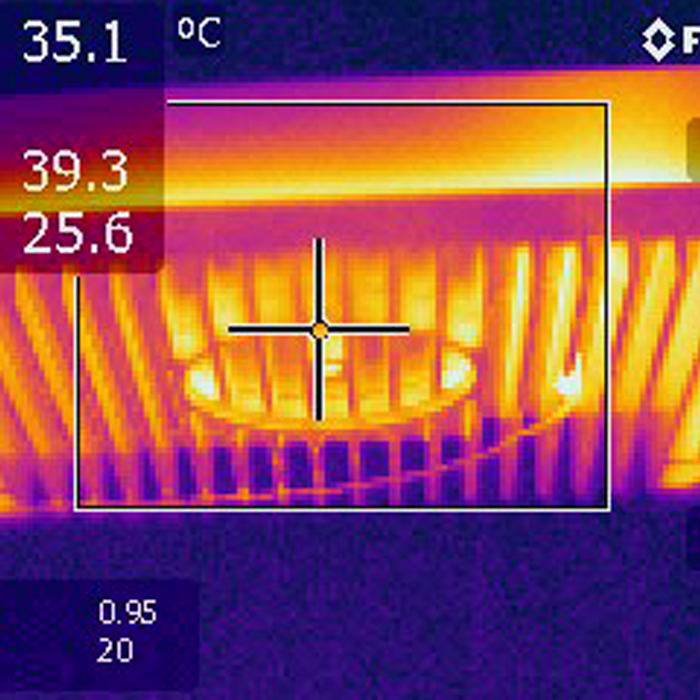
Finite Element Analysis is an important tool used to preempt issues with respect to a components structural integrity. We can simulate forces applied to a part or assembly in advance to understand how the part deforms under certain load conditions based on a specific material. This enables us to identify the weak areas through mechanical stress analysis, fatigue and or vibration to mitigate the risks early in the process.
By identifying these weaknesses early, we can reduce the need for multiple prototype spins or production re-tooling, reducing costs, decreasing the product development cycle and ultimately improving product performance.
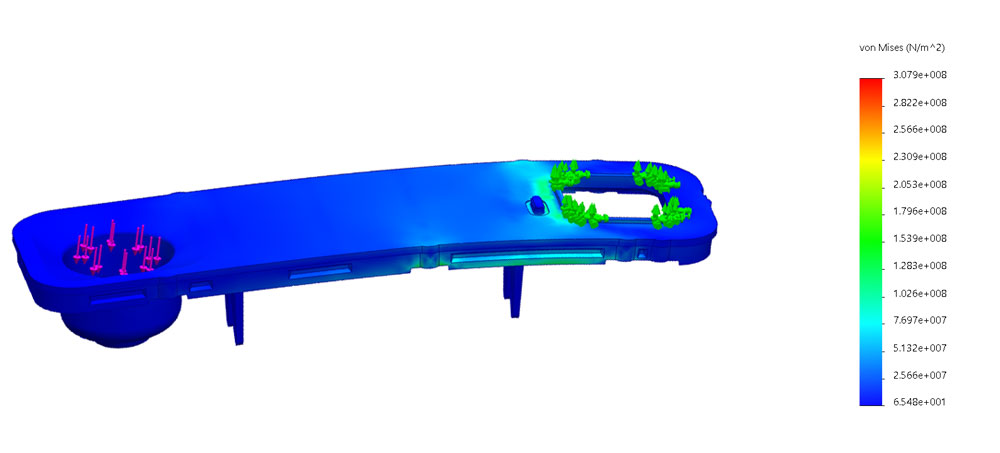
All products and their components require concise 2D CAD specification. Thorough documentation ensures parts and assemblies are made as per intent and within acceptable quality limits. Dimensions, finishes, materials and assembly processes must all be accurately documented.
We have over 50 years of experience at the ‘coal face’ of production. We understand the requirements when specifying parts to suit each and every manufacturing process. From injection moulding plastics, aluminium extrusions to die castings; the design guidelines around each process are very different and critical to achieving a repeatable, high quality part.
We run a Product Data Management (PDM) system for clear and traceable part updates, revision controls and issue tracking.
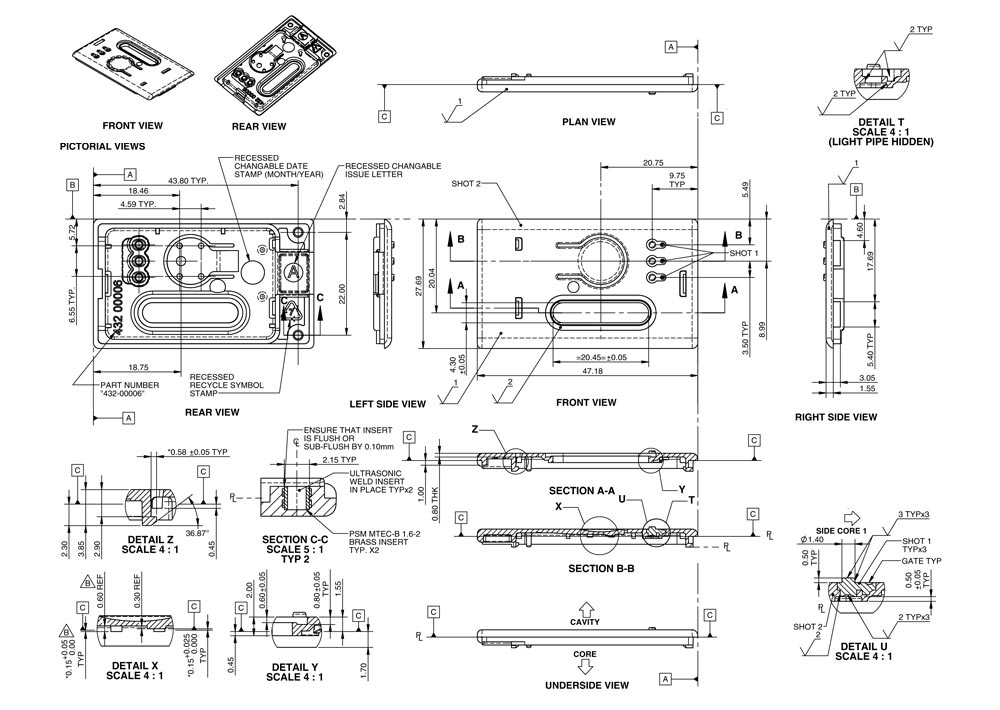